AC Electrical System
Understanding the ATR 72 AC Electrical System
Reading time: 10 mins
Welcome to back to the second iteration of ATR Theory’s technical blogs on the ATR 72-600. Last week, we covered the aircraft’s DC electrical system, you can find that here, so it only makes sense that we move onto the ATR’s AC Electrical systems this week.
Before we jump into the technical gubbins, It’s important you understand that the ATR generates two types of AC (Alternating Current) power. The first being AC CONSTANT FREQUENCY, and the second AC WILD FREQUENCY. The key difference between them is how each one is generated, but we’ll dive into each in more detail later.
Key AC components and their functions are:
Lots of Electrical BUS’s: A ‘BUS’ or Busbar is essentially a big 4 socket extension cable to find at home. However, it has many ‘sockets’ and is crucial to distributing electrical power across the aircraft’s systems. I will add a list of each bus and what it powers at the bottom of the page (if you’re struggling to sleep give it a read).
2 x AC Generators: . One is connected to the Reduction Gear Box on each engine. Frequency of the AC power varies with propeller speed.
1 x TRU: The Transformer Rectifier Unit (TRU) acts like a one way bridge between AC & DC. Whereby the AC system can power the DC side, but not the other way round. It’s used to maintain the batteries when DC power is under emergency supply conditions (Dual DC Generator fail).
2 x Inverters: The two inverters do the opposite job to the TRU as above. They act as a one bridge allowing the DC side to supply the AC side of the electrical system. By converting DC power to AC.
AC CONSTANT FREQUENCY
AC power is an alternating current. Which means that the flow direction of the current changes periodically, accompanied with an oscillating voltage. The number of times a second these two oscillation is measured in Hz. The AC constant frequency oscillates at approx. 400 Hz.
Here’s a schematic of the Constant frequency side of the AC system:
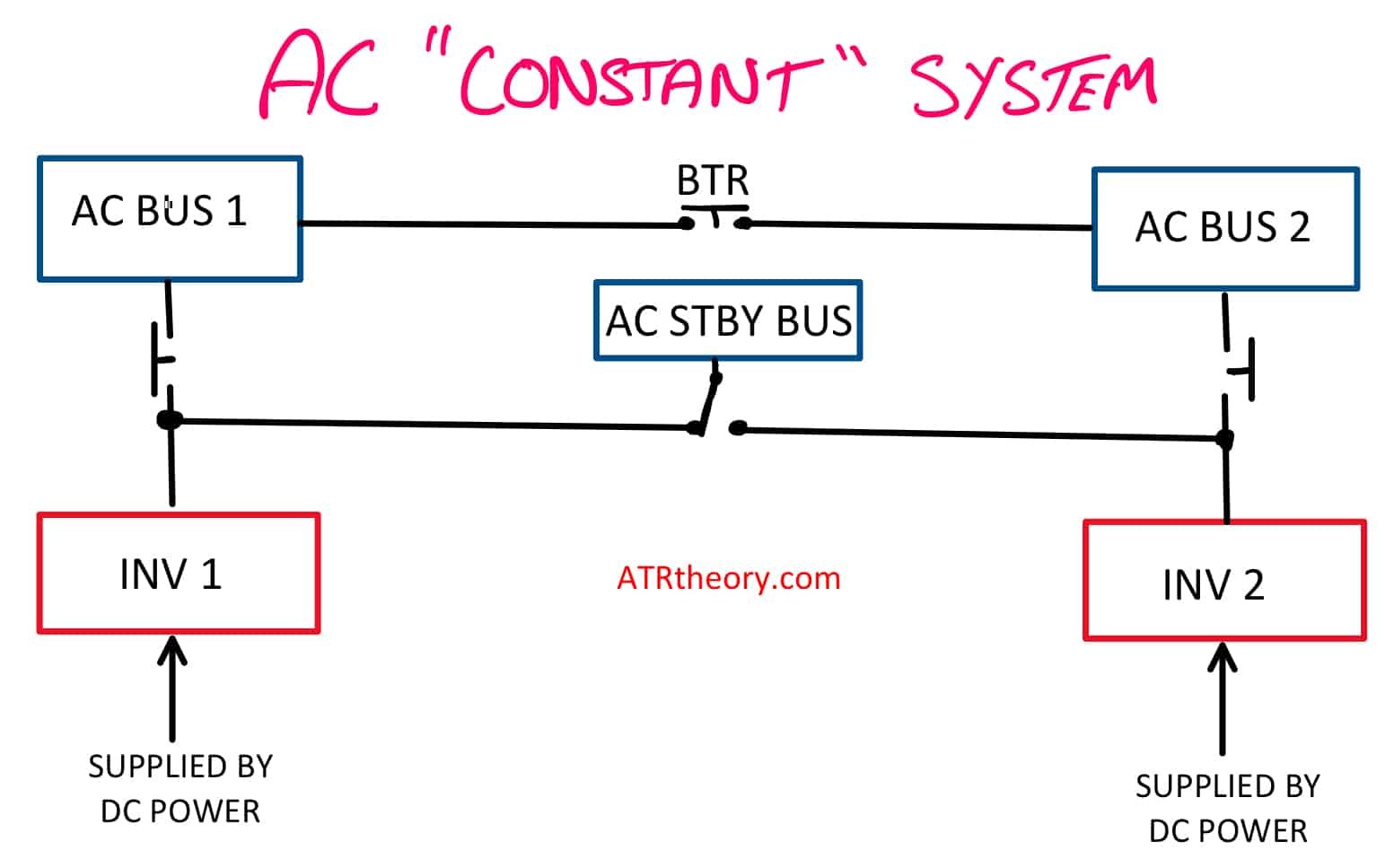
Generation; The source of constant frequency (400 Hz) AC power is supplied via two static inverters. If you read last week’s blog, you’ll know these are an important part of the DC system. An inverters job is to convert power from DC (Direct Current) to AC (alternating current), this is a one-way bridge and power can only be converted from DC to AC, not the other way.
Static inverters don’t actually have any moving parts, and are essentially an electronic switch that takes a DC current flowing in one direction, when the switch is operated it reverses the current to flow in the opposite direction. This electronic switch is operated many times per second, thus creating an alternating current, at a frequency of 400 Hz.
Here’s the technical details for the inverters:
- Power: 500 VA,
- Output voltage: 115 V AC and 26 V AC,
- Frequency: 400 Hz,
- Type: single phase – easiest way to describe phases is to refer back to our switch in the inverter. As this switch operates back and forth converting DC into AC it produces a single wave of AC current. If you have two switches it produces Dual Phase AC, three switches produce Three Phase AC, and so on…
Distribution;
- INV 1 usually powers; AC BUS 1 and AC STBY BUS.
- INV 2 usually powers, AC BUS 2.
Now, in the ATR we have two inverters, each generating single phase constant frequency AC power. These two inverters are powered respectively from DC BUS 1 and DC BUS 2 (see the schematic below). The DC system inputs voltage in the range of 18 VDC and 31 VDC.
In the event of a DC BUS fail, and with 1 inverters not being supplied. The corresponding AC BUS can be supplied via the other via the AC BTR (AC Bus Tie Relay).
****Just to note, In the event of both DC BUS power loss. INV 1 is automatically supplied by HOT MAIN BAT BUS, or by HOT EMER BAT BUS in OVRD config or by TRU when selected ON.
Controls;
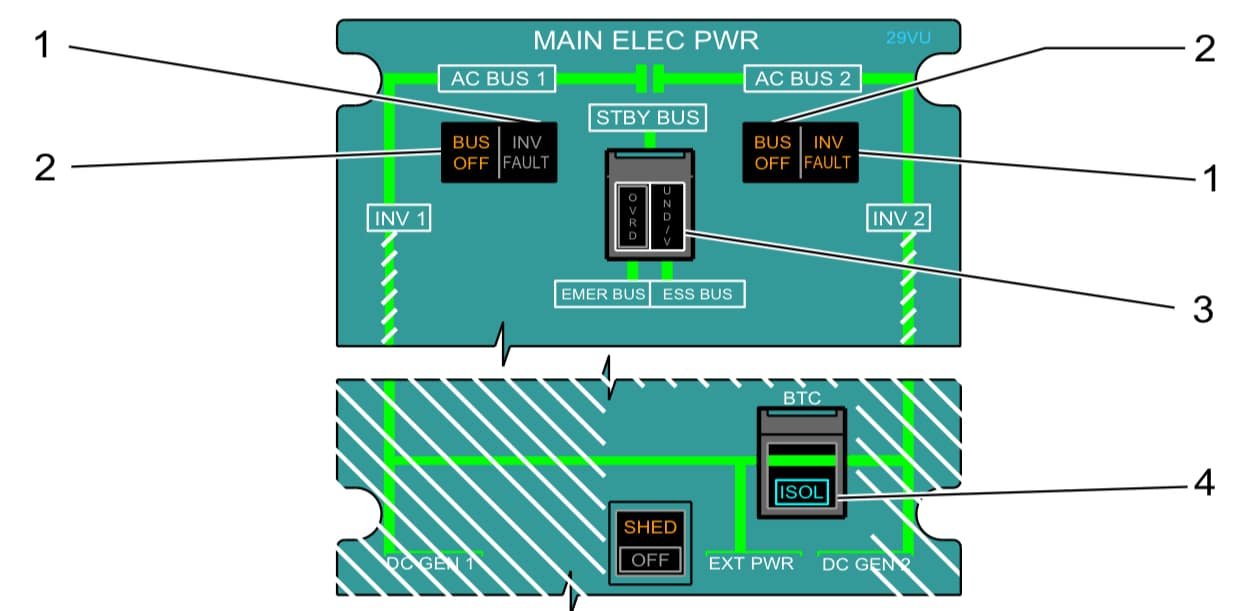
– ATR 72-600 FCOM DSC.24.3
- INV FAULT LIGHT; Comes on amber and illuminates “INV FAULT” in case of an inverter failure or a loss of power supply.
- BUS OFF LIGHT; Comes on amber when associated AC BUS is de-energised.
- OVRD Pushbutton; When on battery supply, this guarded pushbutton enables INV 1 and hence the AC STBY BUS to be transferred from HOT MAIN BAT BUS supply to HOT EMER BATT BUS supply.
- NORM; (button released), the INV 1 and AC STBY BUS are supplied from the same source as DC ESS BUS.
- OVRD; (button pushed in), the INV 1 and AC STBY BUS are supplied from the same source as DC EMER BUS and the OVRD light illuminates white.
- UNDV; This light illuminates amber to indicate that the DC STBY BUS voltage is below 19.5 V. Inverter 1 requires 18 V to operate, so OVRD may be used as necessary.
4. DC BTC pushbutton; This controls the AC BUS TIE relay, which when closed connects both main AC BUSSES.
- NORM; (button released), Automatically open in normal conditions, when both inverters are running, AC BTR is open to separate and isolate both inverter circuits. After inverter failure, the AC BTR is automatically closed after 10 seconds with OVRD UNDV button released. INV fault light illuminates, but BUS OFF turns off after 10 seconds.
- ISOL; (button pushed in); The AC BTR is locked open, ISOL light illuminates cyan.
AC WILD FREQUENCY
The ATR’s AC WILD (ACW) system gets the name “wild” because the frequency it’s produced at is variable. The reason comes from how ACW is produced. The ATR has two ACW generators connected to the Reduction Gearbox, one for each engine respectively. As propeller load varies, so does the rpm of the Reduction Gearbox, thus the rotation speed of the ACW generators also varies, this results is a variable AC frequency being produced.
TLDR; AC frequency is dependent on propeller speed. ACW means that the alternating current is frequency wild, meaning as the generator speeds up or slows down, the frequency of the AC power changes.
Here’s a schematic of the AC WILD System:
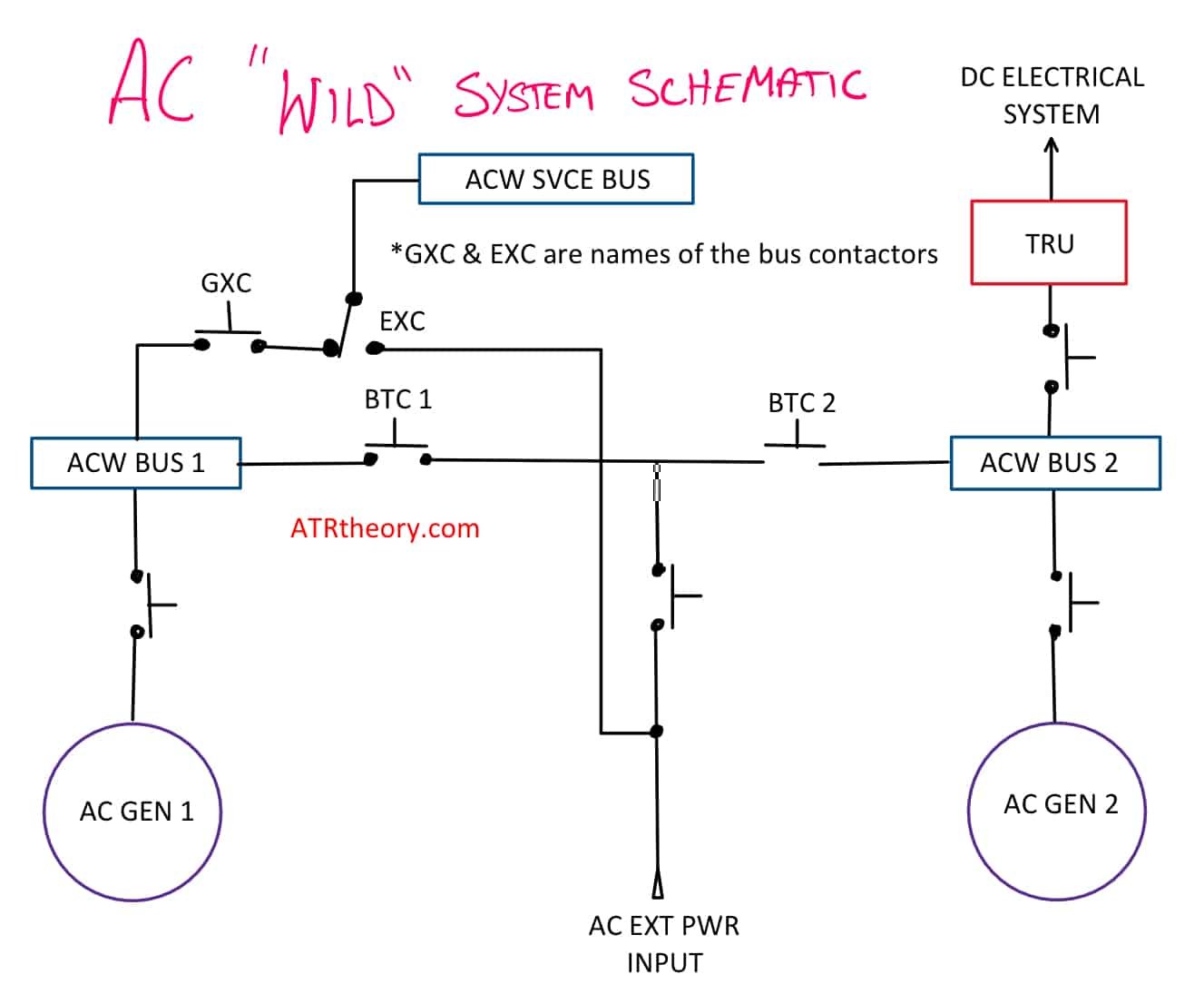
The ACW system supplies power for systems required for taxi and flight such as, taxi & landing lights, hydraulic pumps, and Ice protection. (I will add a full list of systems powered by the AC busses at the button of the blog, (if you need help sleeping :)).
*Propeller Reduction Gear Box; The output shaft connects to a reduction gearbox, which reduces the high– speed rotation of the turbine to a suitable speed for driving a propeller.
Generation; ACW generators consists of two propeller driven three phase generators.
- Voltage produced: 115 V /200 V,
- Operating frequency: 341 – 488 Hz (more importantly remember this is equivalent to 70% – 100%) NP = propeller rotation speed.
Each generator is controlled by a Generator Control Unit (GCU) which provides control and protection functions.
External Power; there are separate input connections for both DC and AC power. Usually in normal operations the ground crew will connect DC EXT PWR. The engineers tend to use AC EXT PWR for aircraft maintenance.
Distribution; the aircraft ACW network consists of three busses; ACW BUS 1, ACW BUS 2, and AC SVCE BUS.
- ACW BUS 1 & 2; ACW BUS 1 is usually supplied by the left generator and the ACW BUS 2 by the right generator. Whenever EXT PWR is connected EXT PWR has priority over the engine driven generators, as long as voltage is in limits.
- ACW SVCE BUS; supplies power in flight, and on ground during airplane servicing operations. The ACW SVCE BUS can be supplied via AC EXT PWR or ACW BUS 1. AC SVCE BUS is controlled via a button on the cabin attendant panel. AC SVCE BUS is automatically shed when one generator is off line.
ACW CONTROL PANEL
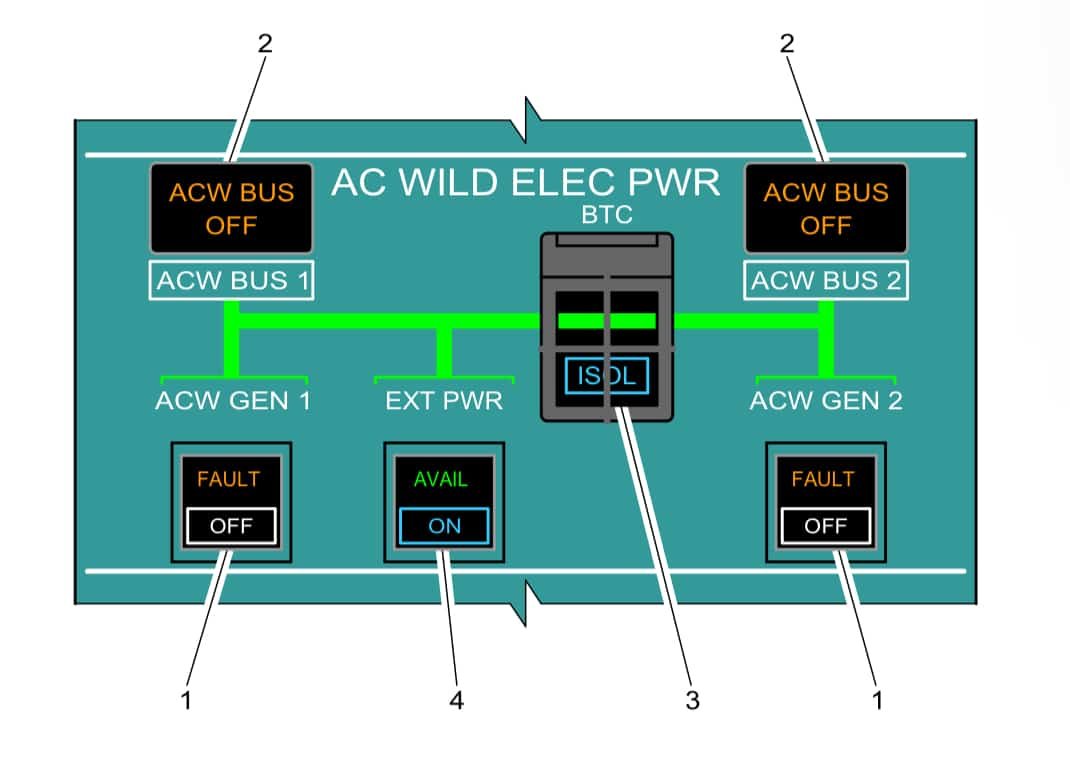
– ATR 72-600 FCOM DSC.24.4
- ACW GEN pushbutton; Controls the energisation of associated generator and the resetting of the protection system after failure.
- Simply, ON turns the generator on & OFF turns it off and disconnects it from the network.
- “FAULT” however, is a little bit different. FAULT illuminates if the contactor unexpectedly opens if the GEN is selected ON. OR if a fault is detected by the GCU, if caused by a generator the GCU will reset it automatically, all other faults have to be manually reset.
After a FAULT the BTCs are closed and affected ACW BUS is automatically supplied from the remaining generator.
2. ACW BUS OFF; light; illuminates when bus is not supplied.
3. BTC pushbutton; this controls ACW BUS TIE CONTACTORS (BTC 1 & 2). When these are closed, they connect both main ACW BUSSES, and the green cross bar illuminates.
- NORM; (button pushed in); in normal operation you won’t use this button, usually it’s pushed in and left that way. The BPCU automatically controls BTC 1 & 2. With engines running, BTC 1 & 2 are open, and enable separate operation of both GEN circuits. With EXT PWR or single GEN failure, the BTC is automatically closed and the green flow bar illuminates.
- ISOL; BTC 1 & 2 are open, “ISOL” light illuminates in cyan.
4. EXT PWR; ACW external power push button. (Mostly used by engineers rather than in day to day operations).
A little more info on the ACW SVCE BUS button; it connects the ACW SVCE BUS to the EXT PWR source or to the ACW BUS 1 when it’s energised.
Well, that’s it for this week’s technical blog covering the ATR 72 AC electrical system. I’ve added a list of the systems powered by the AC busses, for those interested. You’ll find that below. Until next time 🙂
0 Comments